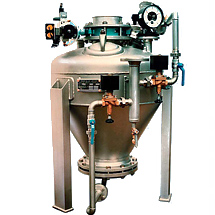
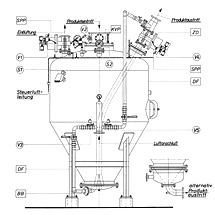
The pressure vessel has established itself for pneumatic conveying with high pressures (long conveying distances) and high product concentrations (high conveying capacities). For poorly flowing products, additional measures (cone aeration, mechanical discharge aids) can be used to increase the conveying capacity. Depending on the product to be conveyed and the conveying distance, gravity discharge (connection of the conveying line below the discharge hopper) or cover discharge (connection of the conveying line from above to a vertical riser pipe projecting into the pressure vessel) as well as different ratios of top, bottom and additional air supply are selected. The pressure vessel can be fed either in free fall or by suitable mechanical conveyors.
The operation of a pressure vessel is always discontinuous, which is why a buffer tank is arranged above the pressure vessel for continuously accumulating material. If high delivery rates are required, two pressure vessels can be operated in parallel. While one is being filled, the other is being emptied. This results in almost continuous conveying. In any case, the amount of material supplied must not exceed the capacity of the pressure vessel. The average availability of a single pressure vessel is 50%, that of a twin pressure vessel approx. 90%.
The achievable conveying capacity of a pressure vessel is decisively determined by the effective volume of the pressure vessel and the diameter of the conveying line. However, due to the often very different bulk weights, grain sizes, grain distributions and other physical properties of the bulk materials, it is not possible to make any concrete statements in advance about conveying capacities with known conveying cross-sections and pressure vessel contents.
Assembly of the MAHR pressurised conveyor system: The conveyor system consists of the pressure vessel with the fully attached fittings. It is connected to the compressed air supply and the electrical control system ready for operation.